14.1. Analysis Process Overviews
In order to calculate fatigue results from RecurDyn/Durability, MFBD model with flexible body should be performed Simulation before applying RecurDyn/Durability. At that time, a point to note is to make Patch Set or Element Set before a simulation. RecurDyn/Durability supports to derive fatigue results only the region which the user defined by using Patch Set or Element Set in the Flex Body Edit Mode. After finishing the pre-requirement processing, the following procedure should be done as so the user can get the fatigue results.
Step to use Durability for fatigue analysis
Analysis a MFBD system with the defined Element Set or Patch Set.
Define several Preferences.
Select the Axial mode for a Fatigue evaluation.
Select Life Criteria among several equations.
Choose Material from the material library.
Confirm a SN curve of the selected material.
Select Element Set or Patch Set of flexible body.
Define Time History for Stress or Strain.
Define Occurrence for Exciting Loading Cycle.
Push Calculation in Fatigue Evaluation Dialog.
Verify the maximum Damage or the minimum fatigue Life.
Confirm Fatigue Results in the Contour Plot.
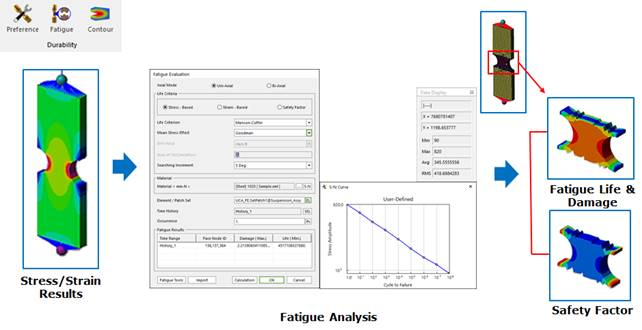
Basically, RecurDyn/Durability supports a lot of criteria which are the equations to calculate the fatigue results from a SN Curve of the selected material.
The supported criteria are as shown in the table below.
Characteristic |
RecurDyn/Durability |
|
Life Equation ( Uni-axial ) |
Stress Life |
1. Manson-Coffin Mean Stress Effect (Goodman, Soderberg, Gerber, Morrow) 2. ASME Mean Stress Effect (Goodman, Soderberg, Gerber, Morrow)
|
Strain Life |
|
|
Safety Factor |
Stress based Fatigue Safety factor
|
|
Life Equation ( Bi-axial ) |
Stress Life |
Bi-Axiality Ratio Method 1. Manson-Coffin Mean Stress Effect (Goodman, Soderberg, Gerber, Morrow) 2. ASME Mean Stress Effect (Goodman, Soderberg, Gerber, Morrow) |
Strain Life |
Bi-Axiality Ratio Method
|
|
Safety Factor |
Stress based Fatigue Safety factor
|
The various life criteria are available to make the SN Curve using the user-defined fatigue material. In the SN Curve, S means the amplitude (or range) of either Stress or Strain cycle, and N means the number of reversals (or cycle) of stress or strain to failure. Among the life criteria in Table 14.1, the SN Curve may vary with the mean stress of the loading cycle. At that time, RecurDyn/Durability identifies the stress or strain amplitude (or range) and the mean stress of each cycle in the stress or strain time history. The damage from each cycle can be evaluated by using the SN Curve of the selected life criterion.
By using the Palmgren-Miner rule which is known as the linear damage rule, the damage from every stress or strain cycle can be summed up to be the total damage. And then, RecurDyn/Durability can calculate the fatigue life by using inverse of the total damage.
Generally, the stress life criteria are available to the application with the high cycle fatigue which is over 10,000. On the other hand, the strain life criteria is useful the application with low cycle which is less 10,000. In case of converting strain cycles into stress cycles or converting stress cycles into strain cycles in order to apply the selected life criteria, RecurDyn/Durability can use the Ramberg-Osgood relation.